Why Choosing a Top-Notch Plastic Mold Manufacturer is Essential for Your Business Success
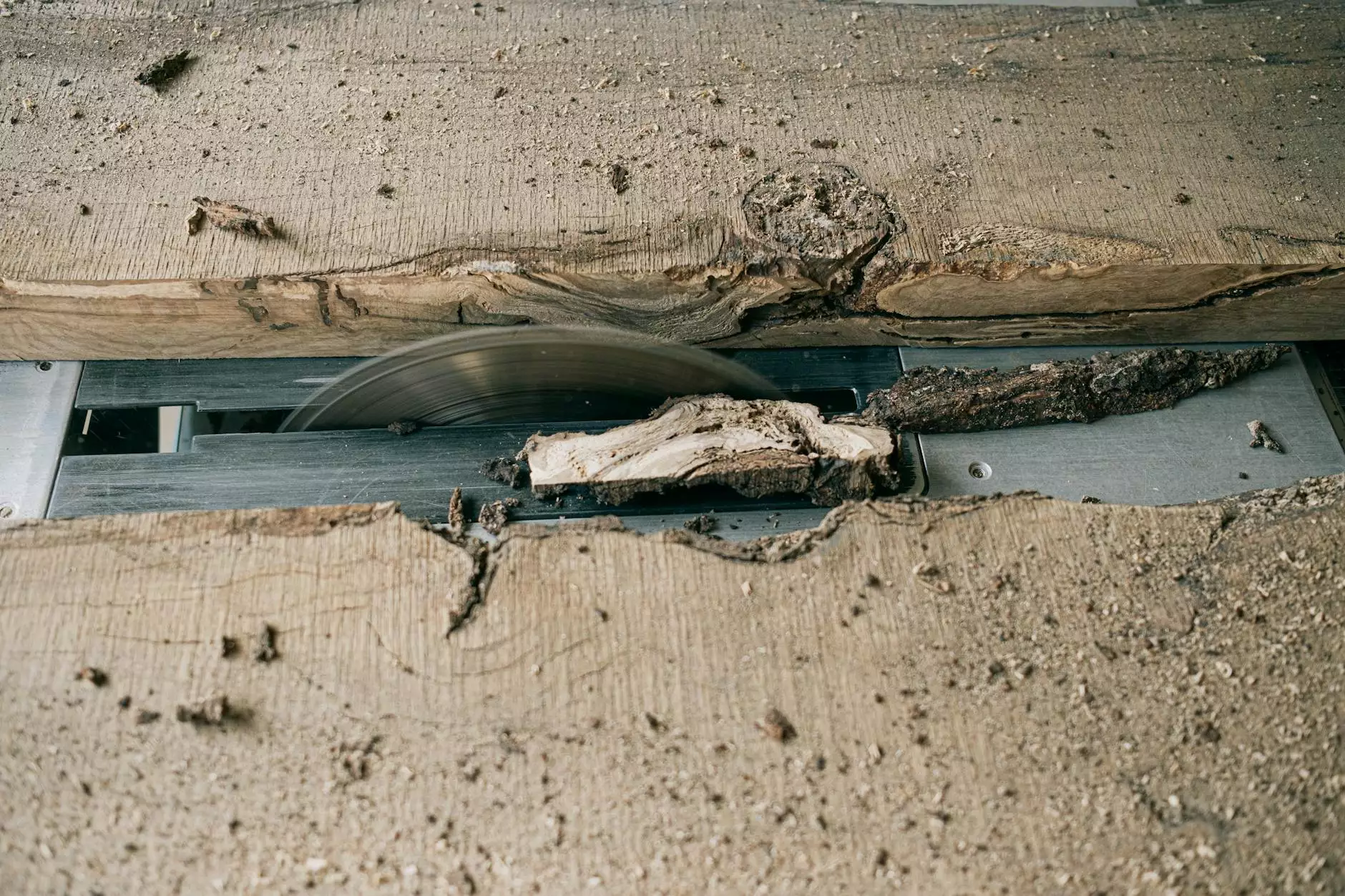
In today’s competitive manufacturing landscape, the choice of a suitable plastic mold manufacturer can significantly influence a company’s operational success and product quality. Molding processes are at the core of producing a multitude of plastic parts that cater to various industries, including automotive, consumer goods, electronics, and healthcare. It is critical to partner with a manufacturer that not only understands your needs but also provides exceptional quality and innovative solutions. This article delves into the pivotal role a plastic mold manufacturer plays and highlights the attributes you should consider while making your selection.
The Role of a Plastic Mold Manufacturer
A plastic mold manufacturer specializes in creating molds that form products by shaping molten material, typically plastic. The process involves several steps, including design, manufacturing, assembly, and testing. Understanding these steps can help you appreciate the impact of your chosen manufacturer’s quality and expertise on the final product.
- Design and Engineering: The initial phase involves concept development and mold design. An experienced manufacturer utilizes computer-aided design (CAD) systems to create precision molds that meet specific product requirements.
- Mold Manufacturing: This step converts designs into physical molds using various materials such as steel or aluminum. The manufacturing capabilities of the provider include CNC machining, electrical discharge machining (EDM), and other advanced technologies.
- Assembly and Testing: Proper assembly and rigorous testing of the molds ensure functionality and durability. A reliable manufacturer conducts quality assurance to prevent defects in production.
Why Quality Matters: The Benefits of a Skilled Manufacturer
Engaging with a proficient plastic mold manufacturer directly correlates with quality and efficiency. Here are the advantages:
- Superior Product Quality: High-quality molds result in better dimensional accuracy and surface finish, which are crucial for the performance of final products.
- Increased Durability: A well-manufactured mold ensures it can withstand high production demands, reducing the frequency of repairs and replacements.
- Cost Efficiency: Investing in quality molds may incur higher initial costs, but they reduce overall production costs by enhancing operational efficiency and minimizing scrap rates.
- Shorter Lead Times: An experienced manufacturer can streamline the mold design and production process, leading to faster time-to-market for your products.
Key Factors to Consider When Selecting a Plastic Mold Manufacturer
Choosing the right plastic mold manufacturer is a nuanced decision. Consider these essential factors to ensure you make an informed choice:
1. Expertise and Experience
Your potential manufacturer’s experience in the industry is a strong indicator of their capability. Look for:
- A portfolio showcasing their previous work in various applications.
- Years of operation and expertise in managing complex projects.
- Certifications or industry awards that attest to their quality and innovation.
2. Technological Capabilities
The manufacturer should employ the latest technology and equipment. Advanced manufacturing techniques are vital for:
- Creating intricate mold designs with precision.
- Reducing cycle times and production costs.
- Meeting high-volume production demands.
3. Customization Options
A manufacturer who offers customization can cater to your unique product specifications. Discuss their capabilities in:
- Providing tailored solutions for specific sectors.
- Working with different materials and mold designs.
- Accommodating varying production quantities.
4. Quality Assurance Processes
A strong commitment to quality assurance is essential. Inquire about their:
- Testing methodologies for molds.
- Certifications like ISO 9001 that express their commitment to quality.
- Use of statistics and data analysis to ensure consistency in production.
Challenges in the Plastic Mold Manufacturing Industry
While the advantages are significant, it is also crucial to recognize the challenges faced in this field:
- Rapid Technological Changes: Staying updated with the latest manufacturing technologies can be a burden, impacting costs and operational efficiency.
- Cost of Raw Materials: Fluctuations in the pricing of raw materials can significantly influence production expenses.
- Market Competition: The global competition drives manufacturers to continuously innovate, sometimes leading to increased costs for clients.
How to Foster a Strong Partnership with Your Manufacturer
Once you’ve selected a plastic mold manufacturer, fostering a collaborative partnership is vital for long-term success. Here are some tips to build that relationship:
- Open Communication: Establish regular communication channels to discuss project updates and expectations.
- Set Clear Goals: Define project objectives, including timelines and quality benchmarks, at the outset.
- Feedback Loop: Provide constructive feedback to empower your manufacturer to exceed your expectations.
The Future of Plastic Mold Manufacturing
The future of the plastic mold manufacturing industry is bright, driven by technological advancements and evolving consumer demands. Notable trends include:
- 3D Printing: The integration of 3D printing technologies for mold-making is revolutionizing the industry, offering rapid prototyping capabilities and lower costs.
- Eco-Friendly Practices: Manufacturers are increasingly adopting sustainable practices, using recyclable materials and implementing energy-efficient technologies.
- Smart Manufacturing: Data analytics and IoT technologies will enhance production processes by facilitating real-time monitoring and quality control.
Conclusion
In conclusion, choosing the right plastic mold manufacturer is not merely about production; it is a strategic decision that can enhance your business capabilities significantly. By considering factors such as expertise, technological abilities, and quality assurance processes, companies can partner with manufacturers that provide not only high-quality molds but also contribute to overall organizational success. Invest wisely in this partnership, and reap the benefits of improved product quality, reduced costs, and a competitive edge in the marketplace.