The Advantages of Laser Welding Cleaning Machines
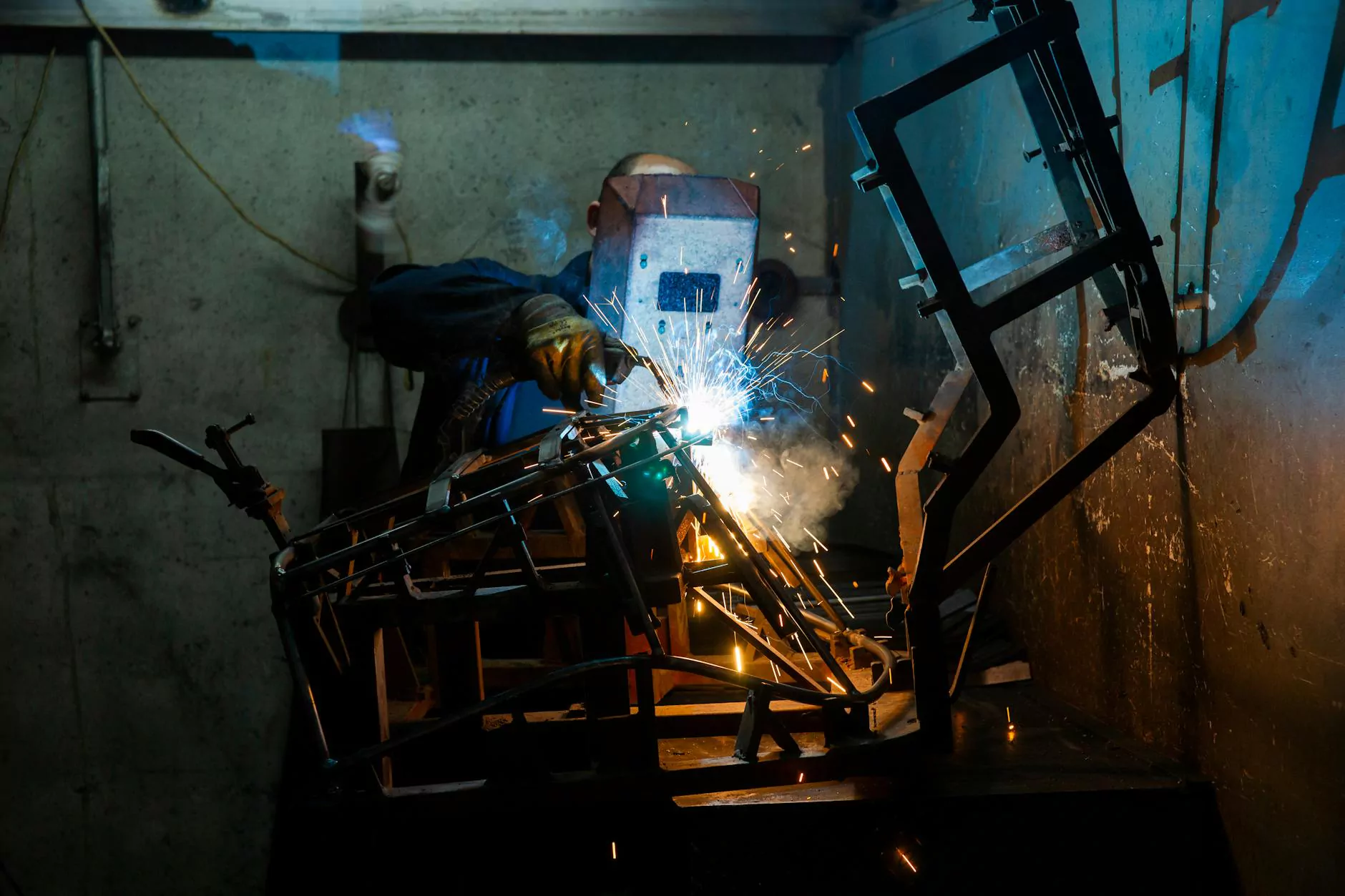
In the competitive world of metal fabrication, the need for precision, efficiency, and cleanliness is paramount. This is where laser welding cleaning machines come into play. These cutting-edge tools offer a range of benefits for metal fabricators looking to enhance their processes and stay ahead of the curve.
Improved Efficiency
One of the primary advantages of using a laser welding cleaning machine is the significant improvement in efficiency it brings to the metal fabrication process. Traditional cleaning methods can be time-consuming and labor-intensive. With laser technology, the cleaning process is not only faster but also more precise, leading to increased productivity and cost savings.
Enhanced Precision
Accuracy is key in metal fabrication, and laser welding cleaning machines excel in delivering precise results. The focused laser beam can target specific areas with unmatched accuracy, ensuring that welds are cleaned thoroughly without damaging the surrounding material. This level of precision is essential for achieving high-quality results in metal fabrication projects.
Reduced Waste
By utilizing a laser welding cleaning machine, metal fabricators can reduce waste generated during the cleaning process. Traditional methods often involve the use of chemicals or abrasives that produce waste and may require disposal. Laser cleaning eliminates the need for consumables, resulting in a more environmentally friendly and sustainable approach to metal fabrication.
Cost-Effective Solution
While the initial investment in a laser welding cleaning machine may seem significant, the long-term cost savings make it a cost-effective solution for metal fabricators. The efficiency and precision of laser technology translate to fewer rework requirements and lower maintenance costs. Over time, the machine pays for itself through improved productivity and reduced operating expenses.
Enhanced Safety
Traditional cleaning methods in metal fabrication can pose safety risks to workers due to the use of harsh chemicals or abrasive materials. Laser welding cleaning machines offer a safer alternative by using non-contact, environmentally friendly technology. This helps create a safer work environment for employees and reduces the potential for accidents or injuries.
Conclusion
Overall, laser welding cleaning machines are a game-changer for metal fabricators looking to streamline their processes, improve quality, and stay competitive in the industry. By embracing this innovative technology, businesses can benefit from increased efficiency, enhanced precision, reduced waste, cost savings, and improved safety. Incorporating a laser cleaning machine into your metal fabrication workflow can lead to a more sustainable, productive, and successful operation.